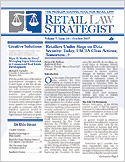
This article was published in the Fall 2013 issue of Retail Law Strategist – a quarterly electronic newsletter that offers practical advice for shopping center professionals. Download the published version: Vapor Intrusion Guidance_published 9.2013 .pdf
On April 11, 2013, the U.S. EPA Office of Solid Waste and Emergency Response (OSWER) released Draft Final Guidance for Assessing the Vapor Intrusion Pathway from Subsurface Sources to Indoor Air (“Final VI Guidance”).[1] Some ten (10) years in the making, OSWER’s draft is out for public review and comment and will serve as guidance to asses vapor intrusion and development and to support risk management guidance. OSWER’s draft Final VI Guidance applies to both residential property and “nonresidential buildings” such as commercial buildings, shopping centers, retail establishments, and industrial buildings where vapor-forming chemicals may be routinely used or stored. OSWER’s Final VI Guidance may impose potentially significant obligation on owners, operators, and managers of commercial property, including retail establishments. As such, buyers, sellers and managers of retail establishments must assess, evaluate and plan for identifying and managing vapor intrusion issues pre and post acquisition.
What is Vapor Intrusion?
Vapor Intrusion is a general term that refers to the migration of potentially hazardous gases (i.e. vapors) into confined spaces such as buildings. Vapors can result from releases of chemicals to the subsurface in both solid and liquid form that migrate through cracks and openings in floors via sumps, pits, and other openings. Significant sources of vapor intrusion include contaminated soils and groundwater underlying an existing or proposed building and can migrate through virtually any type of foundation (e.g. slab, subsurface basement, crawl space, etc.).
In some instances, “free product,” such as petroleum fuels or dry-cleaning solvents can be present in the soil and/or groundwater. When “free product” is present in the environment the risk associated with vapor intrusion can greatly increase. For example, the uncontrolled release of hazardous substances or hazardous wastes in soil can result in these materials becoming located under building foundations. Similarly, groundwater can also be impacted with both “floating” petroleum products and dense “sinking” chemicals (i.e. Dense Non-Aqueous Phase Liquids or “DNAPL”) such as those associated with dry cleaners. In the case of groundwater impacts, free product can migrate over significant distances from “off-site” sources and become located under buildings considerable distances away.
Why is Vapor Intrusion a Concern?
Vapors that volatilize (i.e., become gaseous) can result in human exposure to hazardous and toxic chemicals in indoor spaces. According to EPA, “(v)apor intrusion is widely recognized as a potentially significant cause of human exposure to volatile (i.e., vapor-forming) hazardous chemicals in indoor spaces.” The type of chemical and its relative toxicity can result in health risks resulting from human exposure. Significantly, many volatile vapors, such as volatile organic compounds (VOCs), are also highly flammable and can result in an increase of explosion and fire hazards under some conditions.
Historically, once the initial assessment and investigation were completed as a part of the due-diligence process, little thought was given to the management of future indoor air quality. While a new development may overlay contaminated groundwater, many believed that there would be little or no human exposure to the chemicals if – for example – there were no drinking water supply wells located on the property. Where concerns were raised, EPA recommended that the site be evaluated using the Johnson & Ettinger Model for Subsurface Intrusion into Buildings. Today, the Johnson & Ettinger Model is no longer considered sufficient as the only line of evidence to evaluate the potential for vapor intrusion Although the model is well known, was used as an example in the ASTM risk-based corrective action guide for petroleum hydrocarbons, and is recommended or supported by several states when estimating subsurface soil and groundwater concentrations protective of indoor inhalation, the model does not account for biodegradation, so the results are very conservative for petroleum hydrocarbons and other aerobically-degraded chemicals.
How Do I Assess the Risk Vapor Intrusion into a Retail Establishment?
OSWER issued Draft Guidance on the Assessment of Vapor Intrusion in 2002, and prudent purchasers and sellers of commercial property are increasingly conducting assessments for the potential concerns in the context of real estate transfers and environmental due diligence. While Phase I Environmental Site Assessments (ESAs) are now commonplace, historically vapor intrusion was most often treated as a “non-scope consideration” and beyond the considerations of most environmental consultants.[2]
In 2010, ASTM published a new standard intended for use on a voluntary basis by parties who were concerned about the potential for vapor encroachment and to screen for same.[3] The proposed national ASTM E1527-13 standard practice for conducting environmental site assessments expressly references ASTM’s Vapor Encroachment Screening and requires that “Vapor migration must be considered no differently than contaminated groundwater migration in Phase I investigation. ASTM E1527-13 has two other relevant additions that address Vapor Intrusion. First, ASTM E1527-13 expressly includes “vapor” in the newly added definition of “migrate/migration”. Second, ASTM E1527-13 expressly includes “vapor” in the definition of activity use limitations (AUL). These are significant additions to ASTM and should be carefully considered when evaluating environmental risk management.
OSWER’s “Final” Vapor Guidance was put out for public comment through June 24, 2013 along with companion guidance for releases from underground storage tanks (USTs). In both cases, the guidance “…describes a recommended framework for assessing vapor intrusion that relies upon collection and evaluating multiple lines of evidence to support risk management decisions.” The document is intended for use at any site being evaluated by EPA pursuant to RCRA or CERCLA, Brownfields or State lead sites where vapor intrusion may be a potential concern. The latest guidance presents a tiered analysis that utilizes available and readily ascertainable information to develop an initial understanding of the potential for indoor air exposure and risk posed by vapor intrusion. If no potential for vapor forming chemicals exists in the subsurface or adequate institutional controls are established to prevent development without sufficient additional investigation, then no further action is recommended. On the other hand, a more detailed investigation considering “multiple lines of evidence” is warranted when vapor intrusion exposures are likely to overlying or nearby buildings. Multiple lines of evidence include identified contaminate sources, vapor migration and attenuation, building susceptibility, indoor air assessments, and background assessments.
OSWER has recommended a Vapor Intrusion Screening Level (VISL) Calculator that identifies chemicals considered to be typically vapor-forming and known to pose a potential cancer risk or noncancer hazard through the inhalation pathway; provides recommended screening-level concentrations for groundwater, near-source soil gas (exterior to buildings), sub-slab soil gas, and indoor air based upon default residential or nonresidential exposure scenarios, a target cancer risk level of one per million (10-6), and a target hazard quotient of one for potential non-cancer effects; and facilitates calculation of site-specific screening levels based on user-defined target risk levels, exposure scenarios, and semi-site-specific attenuation factors. According to OSWER, the VISL Calculator can be used in evaluating whether the vapor intrusion pathway has the potential to pose a health concern by helping to identify whether chemicals that can pose a risk through vapor intrusion are present; determine if those chemicals are potentially present at explosive levels; compare subsurface or indoor data against recommended screening levels provided in the VISL Calculator; and prioritize buildings and sites for investigation and response action. OSWER has developed recommended screening-level concentrations in the spreadsheet using the equations and attenuation factors from the Johnson and Ettinger Model, recommended approaches in existing EPA health risk assessment guidance, and current understanding of the vapor intrusion pathway. In other words, OSWER’s new approach represents a more comprehensive approach to addressing Vapor Intrusion.
In addition to the foregoing, it is worth noting that some states (e.g., CA, MA, NY, NJ, and others) have developed guidance for screening and evaluating vapor intrusion, which can be consulted while working in those locations.
Conclusions
Consideration of the risks and liabilities associated with the vapor intrusion pathway can involve complex evaluation of site-specific subsurface conditions, the potential presence of vapor-forming chemicals, and the relative rate of intrusion into overlaying buildings. Such consideration and evaluation should be performed by an experienced and qualified environmental professional familiar with the state of the current practice.
Increasingly, we are seeing more and more developers conservatively assume that vapors may potentially be present now or in the future at new construction sites and to proceed with installation of vapor barriers beneath new buildings. The simplest vapor barriers are simply a layer of plastic sheeting similar to moisture barriers and can be installed at costs of $0.20 to $0.30 per square foot, depending upon the material selected, site location, economies of scale, etc. More elaborate passive soil vapor gas barriers are similar to radon gas barriers and may incorporate a four to six-inch layer of gravel or other permeable material beneath the impermeable barrier, and include vents to conduct the gases to the atmosphere. While, the latter is more elaborate and incur higher costs, it may be only a small traction of the over-all construction cost; the peace of mind the barrier provides against future exposure claims may be well worth the price in many instances. Finally, where vapor-forming chemicals are known to be present in soil or groundwater, active soil vapor gas barriers may additionally include exhaust fans or other forms of ventilation to prevent the build-up of gases beneath a building. In some cases, the treatment of the exhaust discharge might additionally be required.
In all cases where vapor intrusion is expected commercial real estate owners, operators and managers should engage competent environmental counsel and consultants to advise and assess the risks presented. In some instances where sites have been previously “closed,” OSWER’s vapor intrusion guidance may require “re-opening” the site to evaluate whether or not the vapor intrusion pathway has been adequately characterized.
By Michael P. Carvalho, Esq.
CARVALHO & ASSOCIATES, P.C.
Published in Retail Law Strategist
August 2013
[1] Michael Carvalho, Esq. is an attorney who specializes in environmental and real estate matters. His national practice includes litigation, regulatory enforcement matters, and transactional issues associated with the re-development of environmentally impaired real property. He is a former environmental consultant and nationally recognized expert in Brownfield Redevelopment. He is admitted to practice law in Georgia, Massachusetts, Michigan and the District of Columbia. He can be reached at 678-354-0066 or via email. Mr. Carvalho acknowledges the contribution of Steven Hart, P.G. with EnPura, LLC for his technical support in the preparation of this article. Mr. Hart may be reached at 404-210-2917
[2] http://www.epa.gov/oswer/vaporintrusion/documents/vaporIntrusion-final-guidance-20130411-reviewdraft.pdf
[3] See ASTM E1527-05
[4] See ASTM E2600-10